Product Overview
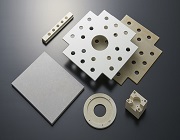
With diverse applications for industrial apparatus or equipment, demand for heat-resistant structure materials has been increasing.
Ryoden Kasei commercially produces “MIOLEX”, a material free from asbestos, which has been highly appreciated by users. With further research and improvement, our “MIOLEX Series” now provides an extensive product line-up.
MIOLEX Series features excellent heat insulation characteristics and mechanical strength, good size stability, outstanding cost performance, the safety of being asbestos-free, electrical insulation characteristics, machinability, etc.
This product fits the environmental measures demanded in recent years because its use leads to advantages such as energy saving and yield improvement.
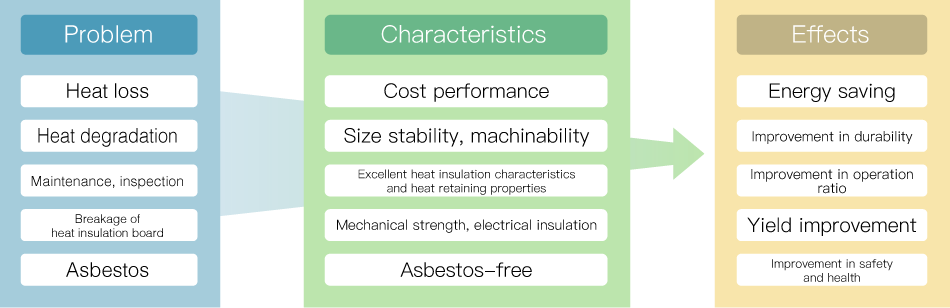
Energy saving effect as a heat insulating material
By using our heat-resistant structural material as a heat insulation board, the amount of heat dissipation from manufacturing equipment can be decreased, and a great energy saving effect can be obtained.
It shortens the temperature rise time at the beginning of operation and reduces material losses during test operation.
As shown in the figure below, with a metallic mold temperature of 140℃, the energy required for heating the metallic mold decreases by about 40% as compared with using no heat insulation board.
The time needed to reach the set temperature is also improved, by about 20%.
Use of a heat-resistant board provides further advantages, such as increasing the uniformity of temperature distribution in the metallic mold, and controlling heat conduction to the molding machine. Consequently, it is possible to prolong the life of both the metallic mold and the molding machine.
Energy saving effect with heat-resistant board
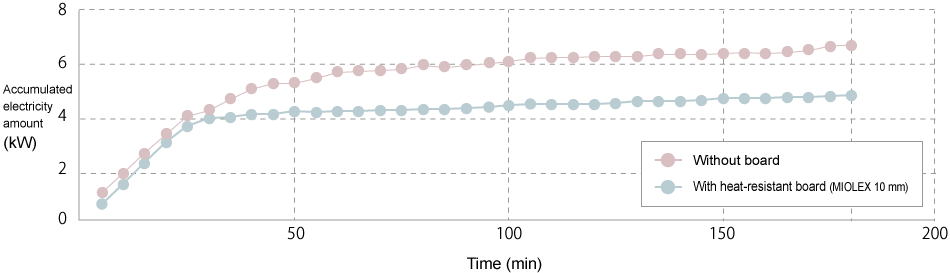
Test machine: 80 ton injection molding machine Metallic mold size: 380 x 320-340 (H) Setting temperature of metallic mold: 140℃ (heated by cartridge heater)
Product Lineup
MIOLEX
Item no | PMX-573 | Heat-resistant property, high cost performance |
---|---|---|
PMX-561 | High heat-resistant property, high cost performance | |
PGX-595 | High reliability: Heat-resistant properties, mechanical strength, size stability |
Heat-resistant glass epoxy laminate sheet
This is a glass epoxy laminate sheet improved with higher strength and heat resistance using our original technology. Its greatest feature is high mechanical strength, which cannot be realized by inorganic materials.
Item no | PGE-6771 |
---|
Characteristics
Physical Properties Image
Compression Strength
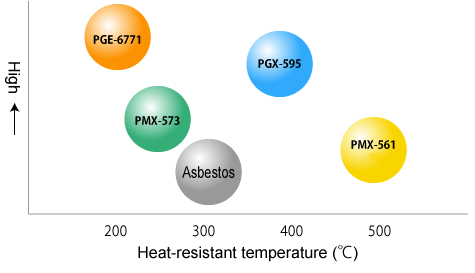
Compression creep
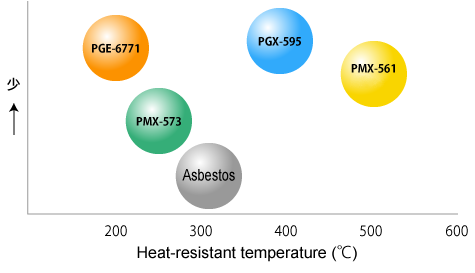
General characteristics
Item | Unit | Pretreatment, Direction | MIOLEX | Heat-resistant glass epoxy laminate sheet | ||
PMX-573 | PMX-561 | PGX-595 | PGE-6771 | |||
---|---|---|---|---|---|---|
Heat-resistant temperature |
℃ | − | 250 | 500 | 400 | 200 |
Compression creep | % | 180℃-10MPa (200hr) |
0.71 | 0.27 | 0.08 | 0.12 |
Bending strength | MPa | A,FW | 100 - 150 | 45 - 55 | 120 - 130 | 450 - 540 |
Compression strength | MPa | A,FW | 150 - 200 | 120 - 150 | 420 - 480 | 500 - 580 |
Impact strength (Charpy) |
J/cm2 | A,FW | 1.5 | 1.1 | 2.5 | 4.5 |
Coefficient of thermal expansion |
1/℃ | A,FW | 6.6X10-6 | 9.0X10-6 | 2.3X10-5 | 6.5X10-5 |
Coefficient of thermal conductivity |
W/(m・K) | A,FW | 0.3 | 0.3 | 0.3 | 0.3 |
Volume resistivity | Ω・cm | ★1 FW | 1012 | 1014 | 1015 | 1015 |
★2 FW | 107 | 109 | 1013 | 1014 | ||
Water absorption | % | After being immersed underwater for 24 hours | 2.0 - 5.0 | 4.0 - 6.0 | 0.1 | 0.05 |
Specific gravity | − | A | 2.0 - 2.2 | 2.0 - 2.2 | 2.0 - 2.1 | 1.8 - 1.9 |
Note | − | − | ◆Incombustible in Material Combustion Test for Railroad VehiclesThickness of 5 mm or more | ◆Incombustible in Material Combustion Test for Railroad Vehicles | ◆Incombustible in Material Combustion Test for Railroad Vehicles Thickness of 1 mm | − |
Explanation of symbols A: As received FW: Perpendicular to the direction of a layer
★1 After drying at 150℃ for 4 hours.
★2 After moisture absorption at 25℃, RH 90%, for 100 hours.
*The values of heat-resistant temperature are just for reference.
*The values in the table are not certified values.
Heat characteristics
Bending strength after 100-hr heat degradation
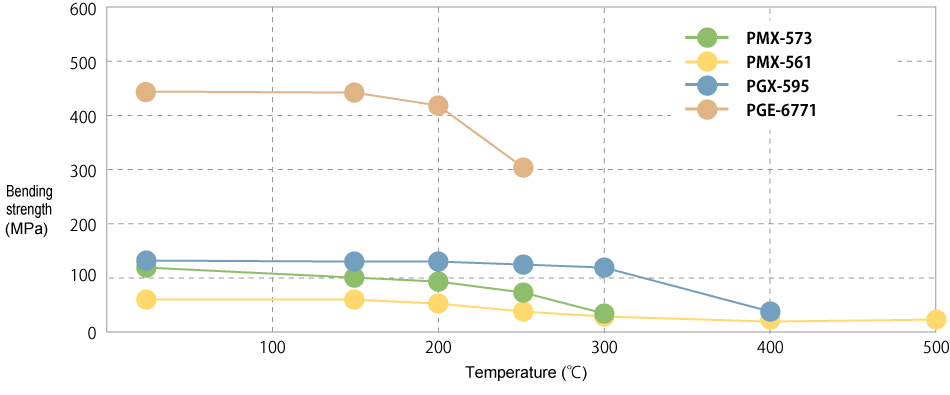
Compression strength after 100-hr heat degradation
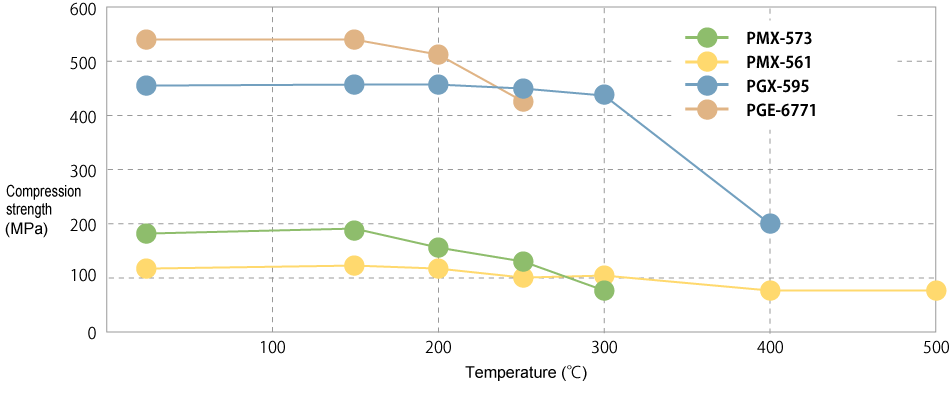
Rate of compression creep (180℃-10MPa: 300hr)
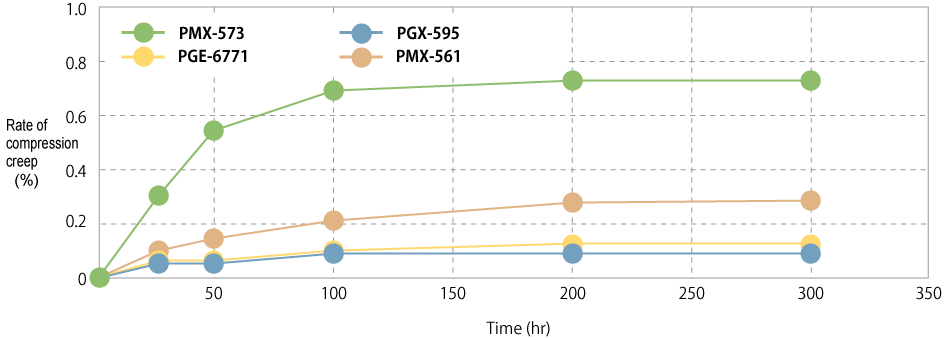
Example of application
Item no | Application field |
PMX-573 | Heat insulation for textile machine, heat insulation for transportation train, heat insulation and heat resistance for general machine and equipment system |
---|---|
PMX-561 | Heat insulation for tire and rubber molding machine, general direct pressure press, heat insulation for metallic mold system, side wall plate of metallic mold for IC device, insulation plate of induction heating furnace and electric furnace |
PGX-595 | Heat insulation for IC molding machine, heat insulation for fine metallic mold, conveyance equipment for electronic device and inspection jig, heat insulation for THIXO casting machine, semiconductor manufacturing equipment, heat insulation for injection molding machine |
PGE-6771 | Heat insulation for injection molding machine, heat insulation for blow molding machine, heat insulation for rubber molding machine, heat insulation for fine metallic mold |
Rubber forming machine (horizontal)
Die casting molding machine
Induction heating furnace
Injection molding machine
Rubber forming machine (vertical)
Standard dimensions
Item no | Thickness (mm) | Standard dimensions (mm) |
PMX-573 | 3 - 30 | 1000 X 1000 |
---|---|---|
31 - 50 | 900 X 900 | |
PMX-561 | 3 - 35 | 1000 X 1000 |
5 - 25 | 950 X 1250 | |
PGX-595 | 1 - 30 | 1000 X 1000 |
3 - 30 | 1000 X 1200 | |
PGE-6771 | 0.5 - 50 | 1000 X 1000 |
0.5 - 50 | 1000 X 1200 | |
3 - 50 | 1000 X 2000 |
*Contact us also for dimensions, thickness, and specifications other than the above.
Cautions for storage and use
General caution | Note |
1. Prevent moisture absorption. |
|
---|---|
2. Pay attention to the atmosphere. |
|
3. Avoid direct sunlight and keep the product in the shade or a cool place. |
|
4. Others |
|